Building powerful and efficient electric motors isn’t enough to create real change in the mobility sector. You need a systemic approach which includes factors like energy-mix and lifecycle design. The energy storage and management systems of Deep Blue are a great example.
Scientists all over the world are working on the future of energy storage. Cambridge’s Massachusetts Institute of Technology (MIT) is developing a solid-state battery that researchers hope will have a much higher energy density than modern lithium-ion batteries. A working group of German researchers at the Helmholtz Institute Ulm for Electrochemical Energy Storage expects sodium-ion batteries to be market-ready in the next few years. And there are other candidates for novel power storage devices: magnesium-air, nickel-zinc, calcium or aluminium. The Swiss research institute Empa is already talking about the age of "post-lithium technologies".
What's behind the multi-billion-dollar research race? While the maximum energy density of Li-Io batteries has more than doubled in the past ten years, the limits of what is technically and physically feasible will, eventually, be reached. "For climate-neutral mobility, we need high-performance batteries charged with green electricity," says Dr Ralf Plieninger, managing director of the world market leader for electric mobility on water. These global research activities are analyzed in detail at Torqeedo headquarters. "Further developments in battery technology will ensure that electromobility is feasible for new fields of application," says Plieninger. "This will increase the proportion of climate-neutral mobility."
There are two reasons for the optimism and certainty that underlies these words: Torqeedo uses high-performance Deep Blue batteries with BMW i3 technology. The modules' capacity has regularly increased – most recently by 34 percent within the same footprint.
The second is that "Torqeedo is a manufacturer of electric drive systems," as Thomas Wiedemann, vice-president program management, says. The system concept is a central component of the strategy: Deep Blue batteries come with a warranty that states that, after nine years, the battery will still deliver at least 80 percent of its original capacity. If that isn't enough and you are ready to upgrade your Deep Blue battery in 2030, you may be able to power your boat with fuel cells or solid-state lithium batteries. "The boat's electric powertrain and energy management system will remain, and you just add new energy storage devices,” Wiedemann says: "As soon as a new technology is ready for the market, our system is ready for it."
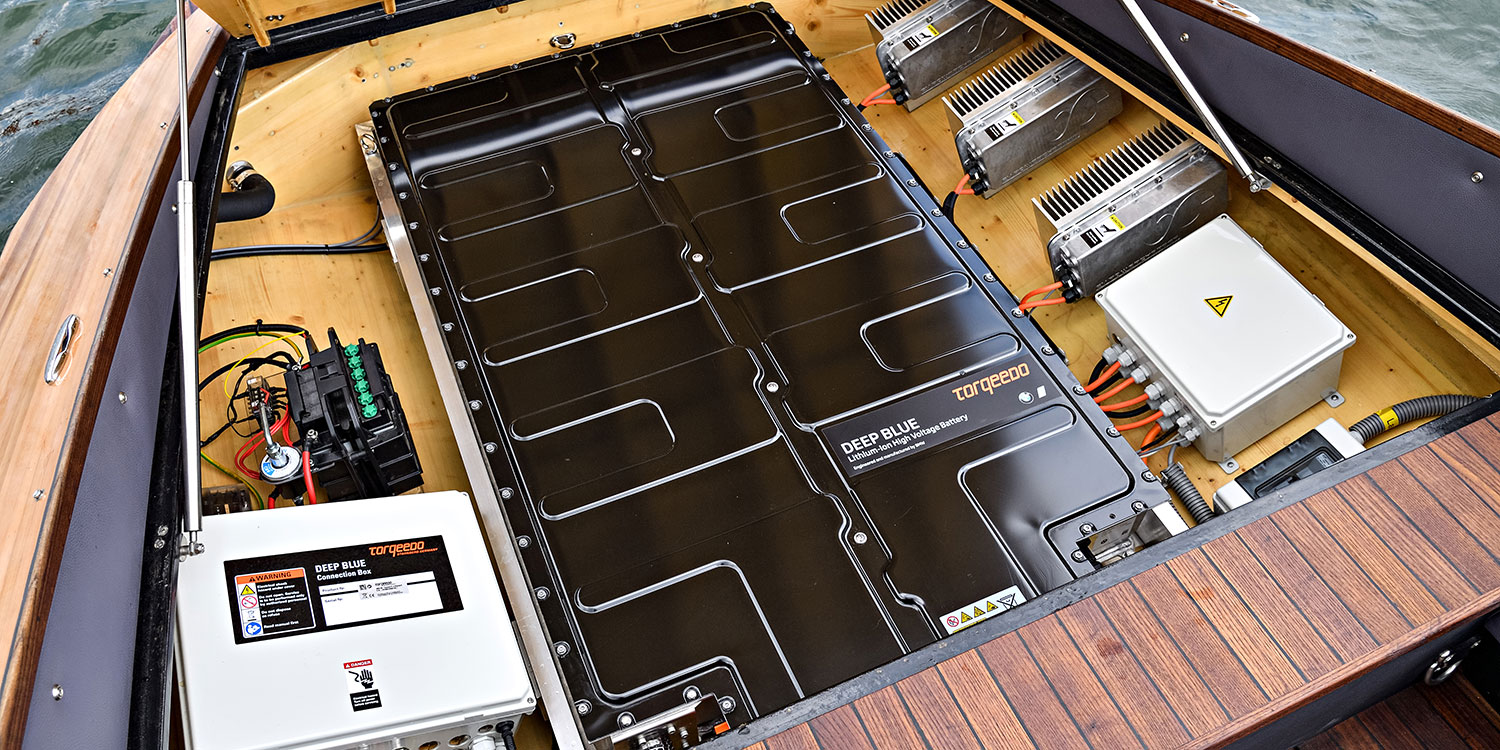
The energy density of batteries has increased significantly in recent decades. What comes next?
Wind turbines on the factory roof
Electromobility is particularly climate-friendly when batteries are produced and charged as sustainably as is possible. "It is a good sign that there are large wind turbines on the factories of our battery supplier BMW," says Thomas Wiedemann. "This is one reason why the CO2 footprint of our batteries is better than that of Chinese manufacturers." But that's not the only reason why Torqeedo has been working with the Munich-based automotive group for years – the batteries produced by BMW have a high energy density, a long service life, and are built to the highest standards of quality and safety. As a bonus, the companies think along similar strategic lines.
"It is important that recycling is considered from the very beginning, in order to establish a closed materials cycle," says Wiedemann, "By partnering with a global corporation like BMW, we can do that. We are also able to do our part to exert a positive influence on supply chains, making sure that metals like lithium and cobalt are extracted and processed with minimal harm to people or planet."
BMW purchases the cobalt and lithium needed for the production of their battery cells directly. Then the cells are manufactured by Samsung to BMW's exacting standards. Taking responsibility for purchasing ensures that the supply chains are transparent and in line with the company's values - and guarantees the security of supply. Together with Samsung, BASF and the German Gesellschaft für Internationale Zusammenarbeit (GIZ), BMW has also launched an initiative for sustainable cobalt extraction in Congo.
BMW plans to achieve a recycling rate of 90 per cent in battery production – which would exceed EU regulations. The BMW Group is working with energy companies such as Northvolt and Umicore to create a closed lifecycle for sustainable battery cells in Europe. There are several steps to consider along the way:
• Battery cells must be designed and installed in vehicles in such a way that they can be easily removed and disassembled after use.
• Batteries should be produced using renewable energy.
• Aging batteries that are no longer suitable for use in the mobility sector should be used as stationary storage systems. At the BMW factory in Leipzig, an energy farm which consists of 700 BMW old i3 batteries is already in operation. The farm compensates for the energy peaks and valleys of wind power generation, storing excess energy in times of high production and distributing it in calm conditions.
• After the battery ages through its second life, more than 20 years after its manufacture, it will be dismantled and the raw materials recovered. The circle finally closes.
According to a study by the German Öko-Institut, by 2030, 10 per cent of the world's lithium and cobalt demand will come from recycling. By 2025, the first batteries used for electric mobility will reach the end of their life cycle, which will finally provide sufficient raw materials to sustain a battery recycling market. By 2050, once that market is established, the study estimates that 50 per cent of lithium and cobalt used will be from recycled sources.
The battery as a capital good
"Batteries have a useful life measured in decades," says Thomas Wiedemann. And that fits very well with the boating sector, where people typically tend to calculate in decades and not - as with cars - in shorter periods. The Deep Blue system tracks battery use and status via the data interface. "There will be a secondary market for batteries," says Wiedemann. "If you use your boat on summer weekends," he calculates, "then you will have 12 to 15 full charging cycles per year. If you're ready to upgrade after five years, you will still have an almost brand-new battery." Due to their high residual capacity, boat batteries will be desirable for energy farms - the battery as an investment asset. The lithium age is not going to end anytime soon. According to a study by the Fraunhofer Institute for Systems and Innovation Research (ISI), higher energy efficiency and improved energy density mean the range of electric vehicles could double in the next ten years.
Behind the scenes: BMW and Torqeedo engineers explain how the Deep Blue batteries are built
If the Torqeedo engineers want to discuss these topics with their BMW colleagues, they don't have to drive far. In the BMW Battery Cell Competence Center in Munich, which opened in 2019, next-generation battery cells are being developed. The focus is on improving energy density, long service life, and enhanced charging characteristics and behaviour at a wide variety of ambient temperatures, a topic that's central to electromobility on the water. In an in-house safety laboratory, battery cells are tested under extreme conditions.
At the BMW plant in Dingolfing, Bavaria, the battery cells are manually combined into modules by electrical engineering experts and welded by industrial robots - a high-precision, high-tech choreography.
High-precision, high-tech choreography
The assembled Deep Blue batteries and battery modules are delivered to the Torqeedo plant 20 kilometres south of Munich. The modules are needed to produce Torqeedo's 48-Volt Power batteries, used in the company's Cruise motor systems. Each battery is tested for watertightness and quality in a final step.
"We really appreciate BMW batteries," Plieninger says, "because they are safe, powerful and of the highest quality."
The cooperation between the two Bavarian technology leaders has been well-established for some time now. "During the integration of the batteries into the Torqeedo energy management system, we invested a lot in optimizing the system," Wiedemann says. For example, Torqeedo's Research & Development department developed a suspension frame that protects the BMW batteries against the shocks that repeatedly occur in maritime use. "We wrote a lot of software to ensure that our system communicates smoothly with the battery via a data interface. That was a big step.”
Clean boating without compromises - that is how it is supposed to be. "These are the great advantages of serial production," says Wiedemann. "The products are reliable, interchangeable and allow upgrades."
More information:
Find high-resolution pictures at the: › Torqeedo Dropbox
Find the main catalogue 2020 here: › Catalogue 2020
Relevant Torqeedo Products
More than a battery
- Commercial
- Big Picture
- Tech